Are the bots on their way to your greenhouse crop?
Added on 16 September 2021
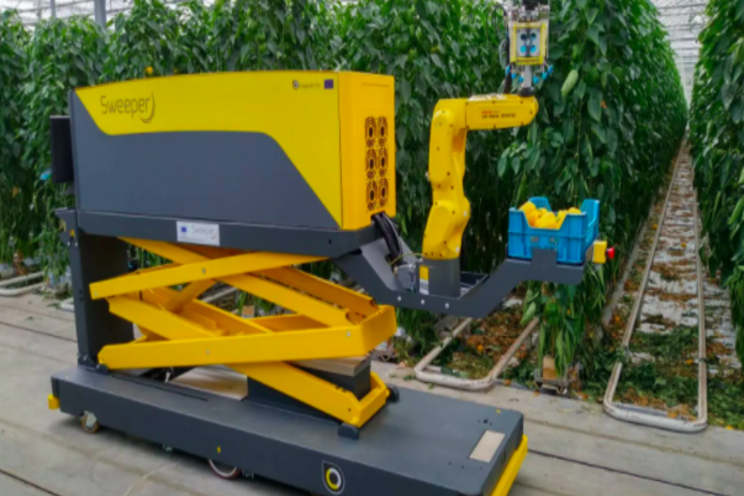
Science fiction? Not according to the researchers and engineers speaking at last year's GreenTech online conference, who see the autonomous nursery as a fast-approaching reality. "Drones are great mobile data-gatherers," said Guido de Croon, professor at Delft University of Technology's Micro Air Vehicle Laboratory.
Ultra light drones as information gatherers
He sees 'swarms' of small, lightweight drones being used in greenhouses to monitor crops for growth and development and signs of pests, diseases, nutrient deficiencies or water stress; and back-up, or replace altogether, fixed environmental monitoring sensors. They could even be used to inspect out-of-reach parts of the greenhouse structure. "They can move in three dimensions to go where needed to gather information, making them much more useful than fixed infrastructure," he said.Agronomists can already include drone images as part of their crop monitoring but in future they will use their expertise to 'train' artificial intelligence (AI) systems to analyse the images and make decisions based on them, said de Croon - there will be just too much data for humans to deal with. "It will be like having the best experts looking real-time into your greenhouse," he said.The drones themselves could respond to the AI, he added. For example, a drone could be sent in for a closer look at a certain bed or an individual plant if the system identifies anything wrong. It would even be possible for each drone to carry a certain level of on-board AI to make such decisions for themselves.His team works with Royal Brinkman and specialises in designing small autonomous drones: one they have developed weighs just 20g but carries a stereo vision system that allows it to judge distances and avoid obstacles. The drones communicate with each other to avoid colliding."Small, lightweight drones are safe for people and generate little downwash [from their rotors], so avoid effects on the crop," he said. "But there is a balance to be struck: the lighter they are, the fewer sensors and less computing power they can carry."
Robots are the doers
If drones are the information gatherers, robots are the doers, performing labour-intensive tasks like picking. Plant-spacing robots already operate on ornamentals nurseries, while several organisations have fruit-picking robots at various stages of development.
Erik Pekkeriet is programme manager for Agro Food Robotics at Wageningen University.
Erik Pekkeriet, programme manager for Agro Food Robotics at Wageningen University, said while more robots are being used they're mostly still 'standing at the front' undertaking tasks such as sorting and grading on conveyor belts, rather than 'running into the greenhouse'.
"But we are quite far ahead now in 3D recognition camera systems," he said. "So we can use robots to do some manipulation, such as taking cuttings or harvesting."
One robot Pekkeriet's team designed was capable of harvesting 90 per cent of a cut-rose crop at the same speed as human pickers - and he suggests that even if robots only harvest the easiest 50 per cent of a crop the labour saved can still stack-up financially, while they also have another role in gathering crop data.
Much of the development for the Wageningen team's 'Sweeper' sweet pepper harvesting robot was done using simulations to 'teach' it what to look for. "Once it was put in the greenhouse it almost immediately started harvesting," he said.
Funding challenges
It is development, rather than manufacturing, costs that are proving critical. Sweeper is based on a standard industrial arm but its vision and AI system is what took most of the project's four million euro of EU funding.
"Small and medium sized enterprises that are the main business model in horticulture can't fund the R&D," he said.
With large corporations from other industries, notably automotive, now taking an interest in AI and robotics for horticulture, that could be about to change.
Greenhouse design and build company Certhon, for example, is now part-owned by Toyota group automotive component manufacturer DENSO, a leader in robotics and process management.
"We're bringing the power of big data and machine learning to horticulture," said Certhon head of business development, Edwin Vanlaerhoven.
"We already have a proof-of-concept robot harvesting tomatoes in a 4ha greenhouse in Japan. We plan to bring it to our innovation centre in the Netherlands for further development, and to involve some big Dutch growers."
It's not just labour costs that will, in the end, drive adoption of autonomous technology: the less human-friendly environments in modern growing systems, reduced crop disease risks from having fewer people working in them, and the potential for greater control over yield, quality and scheduling are important factors too.
"It's not the goal to replace people," says Vanlaerhoven. "We want to give growers better tools and more control."
Source and Photo Courtesy of AIPH
Source: AIPH
More news