Expert input can boost yields for vertical farming
Added on 09 September 2020
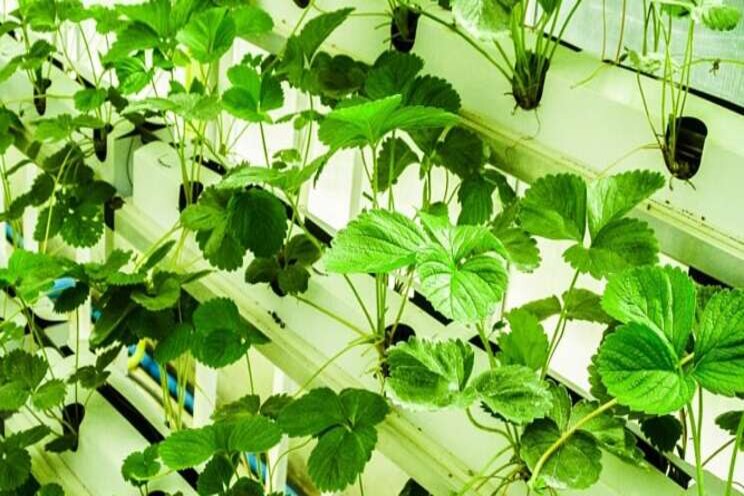
For almost 12,000 years, humankind has found increasingly ingenious ways to convert the natural forces at play on Planet Earth into an ever more bountiful, diverse and predictable source of sustenance.
And, as global and national populations have grown historically and in particular in recent decades, the issue of food security has always hovered somewhere in the background. Today, although we're by no means on the brink of a Malthusian catastrophe, the idea that the UK might at some stage struggle to feed itself has taken on a new relevance.
We've always been used to the supermarket shelves being full. But the early stages of lockdown betrayed the reality that supply chains are highly sensitive not only to the onset of a pandemic but to economic and environmental shocks.
Imperfect storm
Putting COVID to one side, the UK is staring those other two factors square in the face. We currently import approximately 80% of our food, including real basics, such as carrots, but, in Brexit, we are on the verge of a significant dislocation between ourselves and our biggest and closest trading partners who also happen to supply 30% of the total.
And, while Brexit may cause short-to-medium term disruptions, presupposing an eventual agreement on future trade, the risks posed by the environment seem baked in for decades to come.
Extreme weather events, such as significant flooding which has quadrupled since 1980, can harm livestock and spoil crops. On the other side of the coin, water inefficiency and scarcity are issues in many parts of the world, as agriculture competes increasingly with industry and domestic use.
Rising temperatures are playing havoc with growing seasons and sparking ever more wildfires that can devastate farms, even when the flames don't actually reach them.
So, the commercial risks are there for producers. Supply chains are fragile, meaning that businesses dependent on imported produce may be unable to meet the service levels demanded by the supermarkets - even in the short-term - and then scramble for unsustainable and often very costly workarounds.
Removing risk
Vertical farming facilities are the subject of increased interest in the industry. Climate-controlled facilities enable producers to regulate the variables of the environment and avoid pollution to grow produce of a consistently high standard and at predictably higher yields.
The vertical farm projects we have worked on are very hygienic, removing fungal and bacterial risks and the threat from all manner of pests. And, run on LEDs and recycling very high proportions of the water they use back into their processes, energy costs can be minimised, there is no need for water to be chemically treated and producers can extricate themselves from any sense that the taps might one day dry up.
Locally sited facilities mean the vagaries of geopolitics and international trade agreements are no longer an issue. And, as importantly, locating one close to waste-to-energy plant would enable you to harness its heat and CO2 to aid the growing process.
The UK currently imports around 80% of its food
So, vertical farming has a real role to play in helping create circular economies at the local level.
While no means a silver bullet, in our experience vertical farms do solve many of the problems of contemporary food production and have the potential to help brands forge solid reputations as innovators and on sustainability.
But, so great are its potential upsides, one might quite reasonably ask why the shift to vertical farming isn't gathering pace at a steadier rate. The answer, I believe, lies in a perceived lack of expertise in this country at getting such projects off the ground.
A specialist business
For all the simple answers the technology offers, the processes involved are highly sophisticated and capital intensive. Often it is only businesses with the means who go beyond the initial feasibility stages but, even then, they require specialist assistance.
The design and construction of the facilities themselves are highly complex. Different vegetable, fruits and greens each require their own zoning and specific climatic conditions and each of the different vertical levels - up to nine in some cases - has to create and sustain its own unique characteristics.
The electrical and robotic systems running the lighting and hydroponics are as innovative as anything in the sector and that's before one overcomes the challenges of integrating the entire operation.
So, I'd advise companies exploring their options on vertical farming to go back to basics. If you can get those right from the outset and ensure you have continuity throughout the project, you can not only remove risk during planning and construction and for the duration of the facility's lifecycle but also enjoy certainty on cost and programme during the set-up phases.
Ian Hart is business development director at adi Projects
Source and Photo Courtesy of The Engineer
Source: The Engineer
More news