Greenhouse building projects that offer important lessons
Added on 19 June 2020
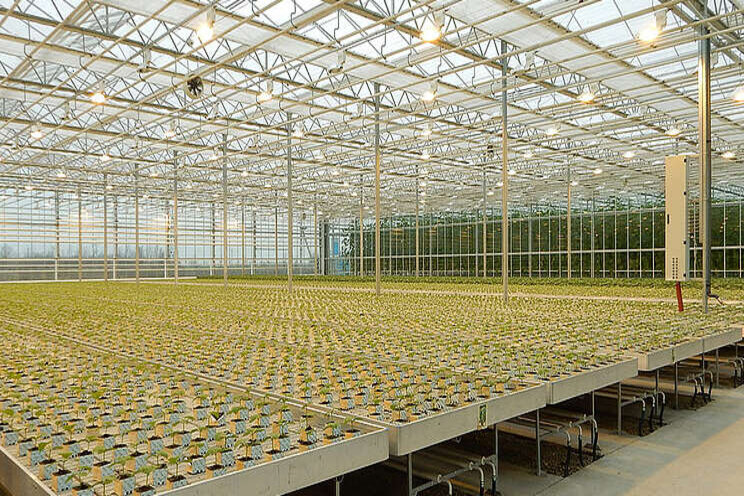
Whatever the case may be, there are lessons to be learned from every new building project. Here's a brief look at a few endeavors taking place in a range of markets, how growers and suppliers worked together to make them happen, and what each learned along the way (check out the slideshow above for a closer look at each project).
Lesson: Know Your Environment
Plant Odyssey, Inc. is a Kyle, TX-based ornamentals producer that has been in business for more than 40 years and is well known for its selection of quality annual and perennial flowering plants, grown under 10 acres of various greenhouse structures.
The company began producing crops using conventional poly and shade houses until its first investment in the early 2000s of a Cravo retractable-roof cooling house. Expansion has been steady in subsequent years, including a recent expansion comprising 5 acres, or half of the nursery.
According to Kent Collum, President of Plant Odyssey, the advantage of the Cravo system is that it uses "the best of both nature and protection to help us produce high-quality plants with vivid colors and dependable shelf life, which ultimately meets the consumer demands of our retail clients throughout the state."
The latest 50,000 square-foot expansion is now in production and features a Cravo A-Frame design with a retractable greenhouse roof, retractable internal cooling/heat retention curtain, and roll-up perimeter walls. All retracting systems are computer controlled to protocols built on Cravo's control strategies (known as the Retractable Roof Production System) developed from best practices over decades of projects.
Lesson: Trust Your Supplier
Saxon Becnel & Sons, a Belle Chasse, TX-based citrus grower, has seen rising demand for its product, enough that owner Ricky Becnel decided it was time for 5 acres of citrus production greenhouses. Aside from the demand, strict regulations on citrus production in Texas due to citrus greening and citrus canker disease make under-cover production critical.
The grower recently worked with Stuppy Greenhouse on a Rainbow Plus structure (four blocks of seven-bay, 30 feet x 450 feet) with 10-foot sidewalls, double vestibule pressurized entries, disinfectant stations, and a perimeter center-roll curtain system.
"We have been building for Saxon for the last 10 years and are able to avoid most technical challenges through a collaborative partnership that thrives on continual customer feedback," says Joel Bartel, Regional Account Manager at Stuppy. "When Saxon wanted to change from its usual 6-foot sidewall to a 10-foot sidewall, our sales and engineering staff took careful consideration to meet the structural requirements of the build, while also making sure we hit all the critical elements of disease prevention as done in previous projects. Saxon also used a new builder for this project, but since our as-built drawings are custom and extremely detailed, the introduction of a new building crew on a large project was a successful one."
"In this case, it was understanding the precautions that are taken daily to grow a clean citrus crop," Bartel says. "From there, we worked backward to find the best greenhouse and equipment solution."
Lesson: Start Small if You Can
Speedling, an ornamentals and vegetable plug producer with eight farms spread out over multiple locations in Florida, Georgia, Texas, and California, has worked with Atlas Greenhouse several times in the past. Recently, Speedling built a 1-acre greenhouse to test different ideas the company could potentially use when it rebuilds its Sun City, FL, location.
"We learned a lot while building this structure, and we're glad we learned on a 1-acre structure rather than one much larger," says Mark Worley, East Coast Division Manager for Speedling. "We still need to experience Florida's summer storms and figure out how well the heating system will work next winter."
Managing temperatures in a new greenhouse build can be a challenge, especially in the south, says Kurt Magstadt, National Account Manager of Commercial Greenhouse Sales with Atlas Greenhouse.
"We put a lot of time into the planning process prior to building the project, and were able to work out a lot of kinks," Magstadt says. "We decided Atlas' Super Arch was the best option partly because it will withstand high wind loads and support a lot of equipment if needed, and is still a cost-effective option."
Lesson: Aim for Dual Uses
Catoctin Mountain Growers recently built a custom shipping dock using a model from Prins USA.
"We wanted a cart staging building that was designed specifically for our cart dimensions," says Tyler Van Wingerden of Catoctin Mountain Growers. "We built it as a greenhouse to use it for growing when we are not shipping, as we wanted a dual-use building."
Lesson: Build With Automation in Mind
Ridder Group and its Canadian partners Anchor Hydro, Zwart Systems, and Acrobat started work in March on a new greenhouse project for Lebo Farms in Leamington, Ontario. The first 30 acres, designed and being built by South Essex Fabricating, are set to be completed by the end of 2020.
Lebo Farms is a new producer of greenhouse vegetables, but the company behind it is no newcomer to the industry. The company was founded by the Leamington-based Neufeld family, who are also the owners of Vine Fresh Acres, a 34-acre cucumber greenhouse facility.
After working with Ridder on the Vine Fresh Project, the Neufeld family went back to Ridder as its main supplier for all intelligent technical components in the new project. All climate control, irrigation, labor registration, climate screen, and drive systems will be supplied by Ridder as one total integrated solution.
Ridder's local partner Anchor Hydro will act as the main contractor and be responsible for the successful installation of all water and electrical systems. The Amherstburg, Ontario-based electrical contractor will supply all Ridder climate control, irrigation, and labor management systems at Lebo Farms.
Greenhouse builder South Essex Fabricating recently broke ground on the first 30 out of 50 acres. It also integrated Ridder RW drive systems and Ridder RES 10 FR energy-saving screens into the design of the greenhouse.
"This project is a great example of how we can supply all key components for a turn-key greenhouse project" says Jamey Barnewall, Canadian Sales Manager at Ridder. "The perfect synergy between all our essential solutions and the commitment of all partners involved will provide Lebo Farms with the best-fit growing solution for their project."
Lesson: Strive for Consistency and Efficiency
Glass House Farms, a cannabis greenhouse in Carpinteria, CA, that was featured on the cover of Greenhouse Grower's February 2020 issue, recently added a new 350,000 square foot facility. Owner Graham Farrar says the California cannabis market continues to grow, so Glass House Farms continues to grow to support it.
"There are more people that consider themselves cannabis consumers than any time in history, and there are more licensed cannabis retailers than ever before," Farrar says. "As people continue to find additional ways that they can enjoy and benefit from cannabis, there is an increased demand, and that all starts with the plant."
The new facility, a System USA greenhouse, was originally an orchid production house that Glass House Farms converted to cannabis. It took almost three years from acquiring the property to the first harvest, but Farrar says it is now up and running and things are looking great.
"We are constantly learning from every project we do," Farrar says. "We improved a lot of things from our first greenhouses and have learned a lot in this one."
Among these lessons are that the simplest solution to get the job done right is the best one.
"You need to always be driving for quality, consistency, and efficiency in everything you design," Farrar says. "Those are the most important components of good operations."
Source: Greenhouse Grower
Source: Greenhouse Grower
More news