Looking to up your controlled environment light intensity?
Added on 24 June 2021
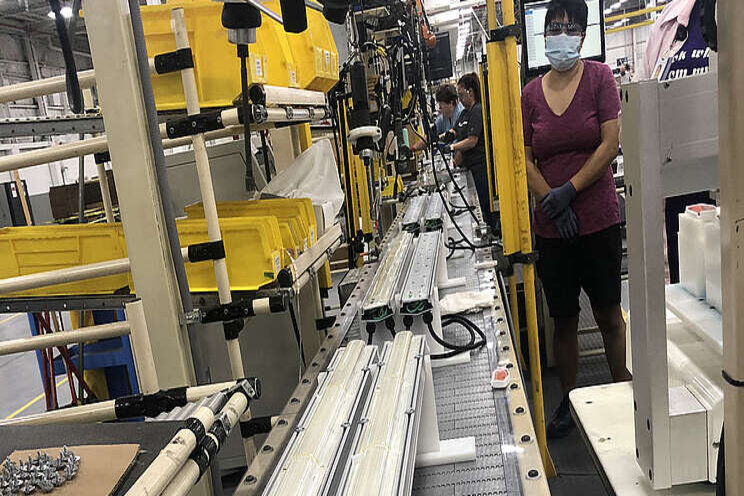
If shortages in the supply chain have you concerned about finding the products you need to produce your crops, the availability of LED grow lights shouldn't be one of them. GE Current, a Daintree company, has started to manufacture its LED grow light fixtures in its state-of-the-art facility in Hendersonville, N.C.
Arize Factor
The first LED grow lights Current has manufactured in its North Carolina plant are its new Factor series.
"I expect the majority of the Factor LED fixtures will be used for vertical farming," said Bruno D'Amico, global product manager, horticulture at Current. "The good thing about Factor is its optics and flexibility, which enable it to be used in other applications. Its wide optics also lends itself well to some shorter head spaces in greenhouses and warehouses."
Factor came out of growers asking for a light fixture that could deliver higher light intensities.
"We were receiving requests from growers to develop a fixture that could deliver more than 300 ?mol/m˛/s," D'Amico said. "Growers were asking for higher light intensities for cannabis as well as leafy greens.
"Once the light intensity starts to exceed 300 ?mol/m˛/s, this isn't necessarily a high or low power fixture, it's kind of in between. That is where Factor comes in. It is a fixture that is very flexible in terms of who can use it. Factor can target light levels as low as 250 ?mol/m˛/s and as high as 1,000 ?mol/m˛/s. The Factor family can be used by large scale leafy greens growers as well as cannabis growers who are looking for a high light intensity either for propagation, vegetative growth or flowering."
D'Amico said Factor falls between Current's Element and Lynk2 fixtures and is available in two power levels.
"The Factor ML300 does very well between 18-24 inches of head space," he said. "It's well suited for growers needing between 300-600 micromoles per square meter. The Factor ML900 works best for higher intensities where growers are targeting 900-1,000 micromoles per square meter.
"For both the ML300 and ML900 Current has nearly doubled the micromole maintenance over time. The L90 is 54,000 hours, which means the fixtures will deliver more consistent light for a longer period of time. L90 means growers can expect to see a 10 percent reduction or loss in light after 54,000 hours."
Because of Factor's wide beam spread (140° over a 4-by-4 footprint), it enables growers to cover more surface area with up to three times fewer fixtures. The dimmable (0-10 volts) fixture also offers growers some versatility regarding installation location. Each light bar can hang independently from top or side hanging bars.
"For indoor vertical farms with under shelves, instead of having to have a fixture every 12 inches center spacing, Factor can extend that spacing up to 36 inches," D'Amico said. "Factor allows vertical farm growers to achieve good uniformity while minimizing the number of light fixtures that need to be installed on the shelves."
Current is also looking at the potential for using Factor in shorter greenhouses with less head space.
"In these tighter situations, greenhouse and warehouse growers who are using 400-watt HPS fixtures may want to consider replacing them with the more efficient Factor LED fixtures," D'Amico said. "The ML900 can uniformly deliver 900 micromoles per square meter which is ideal for lighting cannabis plants."
The Arize Element L1000 LED grow light is Current's one-to-one replacement for 1,000-watt high pressure sodium (HPS) fixtures in greenhouse applications.
Photo Courtesy of Urban Ag News
Arize Element L1000
Current is developing the next generation of its Arize Element L1000 LED fixture, which will begin to be manufactured at its North Carolina plant later this year.
"Element is our top light greenhouse LED lighting fixture," D'Amico said. "The most recent Element product is the L1000. It is a one-to-one replacement for 1,000-watt HPS fixtures in greenhouse applications.
"We are raising the intensity and the efficacy to where growers are going to have the most success with this fixture. This ultra slim fixture will have a more powerful output of up to 2,200 micromoles at over 3 micromoles per joule. Element, which has multiple spectral offers, will match the micromoles delivered by HPS fixtures while lowering operational costs with 40 percent energy savings."
Element is a good choice for growers looking for a high efficiency fixture.
"Current has boosted Element's efficacy," D'Amico said. "Element is well suited for situations where growers are facing either high utility rates and/or longer lighting hours. For cannabis growers who are producing in warehouses, Element's optics and higher efficacy will meet their needs."
Element also comes standard with an optic.
"HPS fixtures are built with reflectors to spread out the light," D'Amico said. "Element comes with one optic which allows growers to optimize light especially with vine crops where head space may be limited. When the head space is 4-6 feet, optics provide the uniformity and help to minimize the number of fixtures. Element allows growers to keep the fixtures to a minimum and still get the uniformity for vine crops where head space is limited."
Current's Arize Lynk2 LED grow light can be used for indoor vertical farming crops including lettuce, leafy greens, microgreens and propagation.
Photo Courtesy of Urban Ag News
Arize Lynk2
Arize Lynk2 is Current's next generation indoor vertical farming precision LED fixture. Lynk2 target crops include lettuce, leafy greens, microgreens and propagation. Lynk2 is ideal for any crop where growers are looking for sub 250-300 ?mol/m˛/s and the head space is limited to 12-18 inches. The fixtures are available in 4- and 8-foot lengths and are can be daisy chained. Lynk2 allows growers to deliver uniform, targeted, precision lighting.
Although Lynk2 is not manufactured at Current's North Carolina plant, this grow light is built off the legacy that the company had with Lynk, which was its first indoor vertical farming fixture.
"Lynk was widely used by many large vertical farms including Mirai in Japan and Jones Food Co. in the UK," D'Amico said. "All the lessons learned from using Lynk in those operations and the feedback from our customers went into building Lynk2."
There were three major updates that Current made with Lynk2.
"We have increased the efficacy of Lynk2, which now surpasses 3 micromoles per joule," D'Amico said. "This is particularly important when considering the amount of energy used in sole source lighting as in vertical farms. Lynk2 can help growers avoid having to spend more money on utilities."
Another feature that was added to Lynk2 is dimming.
"Lynk2 has a 0-10 volt dimming functionality that allows growers to tailor the light intensities for their specific operations," D'Amico said. "This dimming feature, which is a lighting industry standard, enables growers to light where they want at the intensities they want."
Another thing that Current improved in Lynk2 is its optics.
"Current has 20+ years of experience working with LEDs across a lot of different categories," D'Amico said. "That has enabled us to learn about optics, which we design in-house.
"The optics on Lynk2 are wider so the fixture produces more uniform light. Delivering the same amount of light from edge to edge on the surface of the plants allows growers to have better quality control. This means every crop is going to be uniform, which is a real a benefit when growers go to sell their crops."
Another significant improvement that Current made to Lynk2 is its lumen maintenance.
"We've improved significantly to nearly 2x Lynk2's micromole maintenance," D'Amico said. "The L90 is 54,000 hours, which previously was an L90 of 36,000 hours. For growers this means more consistent light for a longer period of time. Growers can expect to see a 10 percent reduction or loss in light after 54,000 hours, which is very good."
Advantages of U.S. production
D'Amico said the advantages of building the Factor and Element grow lights in Current's North Carolina manufacturing facility include product availability and delivery.
"This factory is built around just-in-time manufacturing," he said. "This is especially important for just-in-time orders for growers and installers. Growers who are installing lights in a 1- to 10-acre facility, managing all the logistics as to when the lights will be delivered and installed can be a lot of work and can be costly. Particularly for large operations, this means ordering the lights in bulk and having them delivered and having to store them near the facility so they can be installed.
"The advantage of manufacturing the fixtures in North Carolina is the plant is within five-day transit of anywhere in North America. This means we can work with growers to manufacture the fixtures so that we can ship them when they need them. Looking at the logistic costs and the savings that can be realized, it can add up quickly for growers."
For more: GE Current, a Daintree company, Dan Lee, (216) 375-4618; Daniel.Lee3@gecurrent.com; https://www.gecurrent.com/horticulture.
If you are attending this year's Cultivate'21, July 10-13 in Columbus, Ohio, be sure to stop by the Hort Americas trade show booth (No. 2421) to see and learn more about Current's LED grow lights.
Source: Urban Ag News
Header Photos courtesy of GE Current, a Daintree company
Source: Urban Ag News
More news